Stationary Batteries play a crucial role in various industries, ensuring reliable and uninterrupted power. However, these systems, particularly those utilizing Valve Regulated Lead Acid (VRLA), Vented Lead Acid (VLA), and Nickel-Cadmium (Ni-Cad) batteries, pose potential safety hazards due to hydrogen gas generation. This gas is produced during normal operations and can increase significantly during charging or under abnormal conditions. If not properly managed, hydrogen accumulation can lead to catastrophic events such as explosions and fires. Lithium-Ion batteries do not produce hydrogen in normal operation, but release hydrogen in abnormal conditions such as thermal runaway. In this blog, we explore the risks associated with hydrogen in battery storage systems, the industry standards for mitigating these risks, and the advantages of hydrogen monitoring systems over traditional continuous ventilation methods. Here is a summary of the importance and best practices of hydrogen sensors for battery rooms.
Battery Technology and Hydrogen Release
- Valve Regulated Lead Acid (VRLA) Batteries
VRLA batteries are spill-proof and designed to minimize water loss through a recombination process. However, during recharging, charge equalization or any irregular charging situation, this valve may open, releasing hydrogen into the surrounding environment. This release is often caused by overcharging which can leading to thermal runaway—a self-sustaining rise in temperature that can increase hydrogen emission from the battery. - Vented Lead Acid (VLA) and Nickel-Cadmium (Ni-Cad) Batteries
VLA and Ni-Cad batteries are characterized as gassing batteries by their ability to vent gases produced during charging. Hydrogen production is highest during charging and reaches its peak when the battery is 90% charged. Overcharging or and boost charging can lead to excessive gassing. Though rare for vented batteries, abnormal conditions can lead to thermal runaway, further increasing hydrogen emissions. - Lithium-Ion Batteries
Lithium-Ion batteries, though generally sealed, can emit hydrogen and other flammable gases during a thermal runaway, which may be caused by internal short circuits, overcharging, external heat and other types of abuse. These batteries rely on a Battery Management System (BMS) to regulate their operation, but the BMS can also be susceptible to sensor failures, software glitches, rapid temperature rise and complex fault scenarios - Iron-Air batteries
Iron-Air batteries generate hydrogen during the charging process when water is electrolyzed. To manage this hydrogen, recombination catalysts or venting systems are used. Additionally, hydrogen sensors are often integrated into these systems to monitor gas levels and trigger appropriate safety measures.
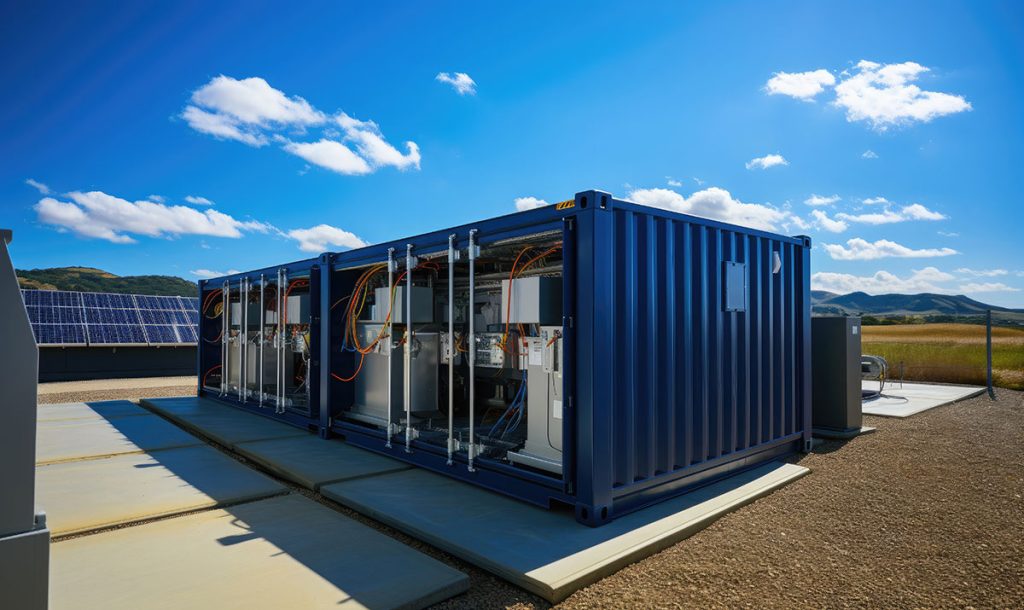
Battery Storage Industry Best Practices and Standards
Industry best practices and standards have been established to mitigate the risks associated with hydrogen generation in battery systems.
IEEE Standards for Battery Room Safety
The IEEE 1635/ASHRAE 21 standard provides guidelines for managing hydrogen evolution based on battery type and outlines the potential heat and off-gassing varieties. For example, VLA battery rooms can experience a 2% increase in hydrogen concentration after just half a day of equalized operation and three days of normal float operation. This standard is essential for understanding the risks associated with different battery technologies and implementing appropriate ventilation and monitoring systems.
Fire Codes and OSHA Regulations
The IEC 62933-5-2 is a standard developed by the International Electrotechnical Commission (IEC) that focuses on safety requirements for grid-connected energy storage systems (ESS). This standard is crucial for ensuring the safe operation of energy storage systems, which are becoming increasingly important in modern power grids.
Fire Codes and OSHA Regulations
Fire codes, such as those outlined by the National Fire Protection Association (NFPA) and the International Fire Code (IFC), mandate specific safety measures for battery storage systems. For instance, the IFC requires that battery rooms containing more than 70 kWh of energy storage adhere to stringent fire code regulations. Hydrogen sensors and detection systems are crucial in these settings, as they can trigger mechanical exhaust ventilation when hydrogen levels reach a certain threshold.
Real-World Incidents: The Importance of Proper Hydrogen Sensing and Management
Several real-world incidents underscore the importance of proper hydrogen management in battery storage systems. For example, in Los Angeles in 1994, a hydrogen ignition at a telephone exchange caused the loss of 911, police, and fire communications for an hour. The incident involved six strings of VRLA batteries wired in parallel, and the ignition of hydrogen at one battery post triggered a chain reaction.
In another incident in 2001, a hydrogen explosion in an Uninterruptible Power System (UPS) battery room caused significant structural damage to a decommissioned data center. Although a hydrogen monitoring system was in place, it remained unclear whether the ventilation system was operational when the building was evacuated. These examples highlight the critical need for robust hydrogen monitoring and ventilation systems to prevent such disasters.
New vs. Old Technology: Advancements in Hydrogen Sensing and Detection
Traditional hydrogen sensing technologies for battery storage, such as catalytic bead sensors (CBS) and thermal conductivity detectors (TCD), have been widely used for area sensing. However, these technologies require frequent calibration and replacement, leading to higher maintenance costs. Moreover, TCDs are not component-specific and can be cross-sensitive to other gases, reducing their reliability in detecting hydrogen.
In contrast, new solid-state, auto-calibrating hydrogen sensors offer several advantages. These hydrogen sensors do not degrade over time, providing a longer service life of 10 to 15 years. The drift-check feature in these sensors eliminates the need for manual calibration, reducing maintenance requirements and ownership costs by up to 40%.
More details are available in our full white paper Managing Hydrogen Risk in Energy Storage & Battery Backup Systems. Contact us to talk to an applications engineer about hydrogen sensor solutions for your data center, battery storage and other energy storage areas.