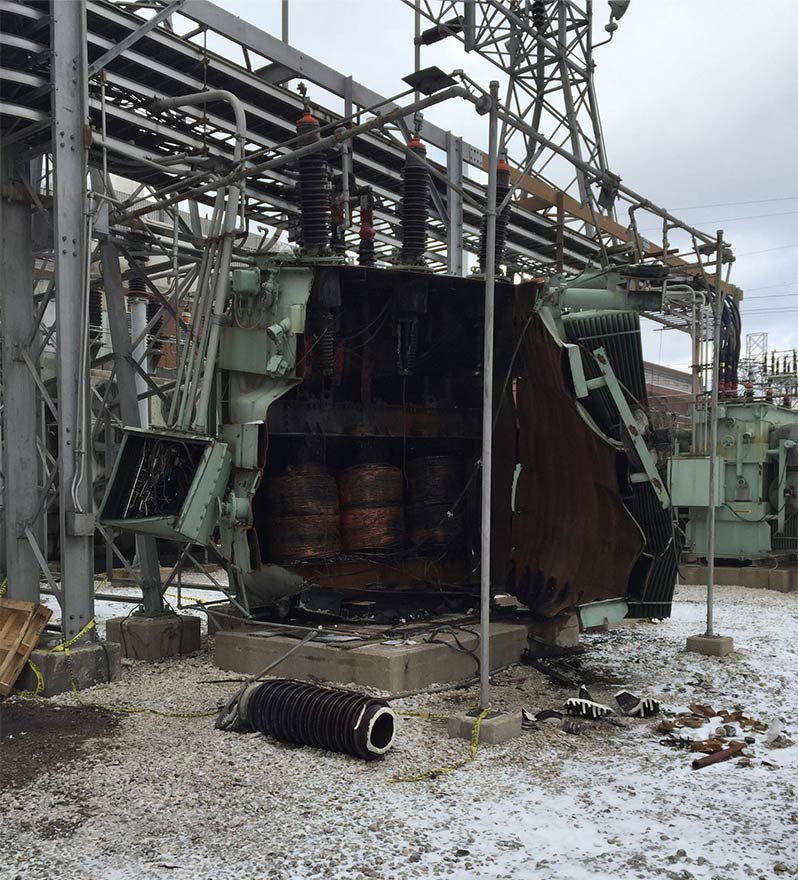
Can You Predict Your Next Transformer Failure?
Few can forget the Camp Fire wildfire in California in 2018, sparked by faulty electrical infrastructure and spread by strong winds. In addition to 85 lives lost, a German insurance company estimated the total damage from that single incident to be $16.5 billion. Unfortunately, it wasn’t the first, nor will it be the last such destructive and devastating wildfire. Numerous studies and research by both governmental bodies and non-governmental organizations attribute a portion of the frequent wildfires seen in recent years to aging electrical infrastructure.
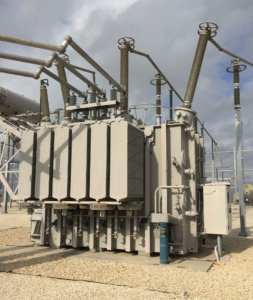
transformer fleet.
These organizations also document utilities’ struggles to prioritize updates. While the lines, poles and brush are major concerns, the transformers can also cause problems. Yet there is an easy and cost-effective means to proactively prioritize where infrastructure dollars should be spent first as part of a “technology-forward” approach to monitoring and predicting transformer health for equipment of any age, supplying the data utilities need to proactively address issues before disaster occurs.
Transformers and Their Critical Role in Supplying a Steady Power Source
One of the worst nightmares for any electric utility or industrial facility manager is a sudden transformer failure, particularly when the technology exists to eliminate “sudden” surprises. When a transformer goes down, outages can be costly, not to mention potential safety hazards. The consequences can range from an inconvenience to millions of dollars in losses for companies relying on a steady power supply.
Unfortunately, transformer failures are all too common. Cost pressures have led manufacturers to make newer units smaller and with less insulation margin, increasing the chances of premature failures. While older transformers were built with more robust insulation and a greater tolerance for electrical and thermal stresses, newer transformers don’t have these advantages. The inferior new transformers are becoming increasingly more common as aging infrastructure continues operating past its designed lifespan and power grids expand, requiring more transformer installations. And, to make replacing transformers even more difficult, the waiting period for new equipment can be up to two years.
On top of the age factor, transformer failures can strike without warning due to various causes like insulation degradation, manufacturing defects, overloading or electrical transients and harmonics from renewable energy sources like solar farms and wind turbines. Solar farms produce DC power, which requires an inverter to convert to AC for the grid. The inverters create harmonics. In fact, the solar and wind power industries can witness transformer failure rates as high as 50% within the first few years of operation at some installations due to harmonics issues alone.
The Hidden Costs of Transformer Failures
While the direct costs of replacing a failed transformer are substantial, there are also significant hidden costs and risks that make preventing failures even more critical. Depending on the facility or operation, the costs of process downtime from a transformer outage can dwarf the actual transformer replacement costs.
For example, a utility may need to pay hefty regulatory fines if a transformer failure causes prolonged outages and violates reliability standards. In manufacturing facilities, critical process operations can grind to a halt when transformer power is lost, resulting in costs from wasted product, missed deliveries, employee downtime and more. Across industries, transformer failures put personnel at risk from hazards like fires, explosions and mishandling during emergency replacement efforts.
Environmental costs from transformer failures are another major consideration, especially for companies under increased scrutiny and regulations around sustainability goals. A catastrophic failure of an oil-filled transformer can result in mineral oil spills that are extremely difficult and expensive to remediate. There are also emissions impacts – when electric utilities lose transformers, they must ramp up backup generation from higher-polluting sources to compensate.
Beyond just replacement costs, transformer failures create a cascade of negative operational, safety and environmental impacts. This makes a compelling case for any company to invest in affordable monitoring solutions that provide early warning and prevent these incidents from occurring in the first place.
Don’t Be Caught Off Guard
The old reactive approach of “run to fail” is becoming increasingly unacceptable as the costs of outages skyrocket and the replacement lead either involves a long lead time or risks inferior quality from some overseas sources. Waiting for a transformer to completely fail and then scrambling to get a replacement is a massive disruption that no business or utility can afford.
So, how can facility and fleet asset managers avoid being blindsided by a catastrophic transformer failure? And can a transformer failure be predicted? The simple answer is yes—transformer failures can be predicted with the right monitoring tools and practices in place. While unplanned failures will not completely be eliminated, there are monitors and hydrogen sensors available to provide advanced warnings needed to stay ahead of developing issues.
Some companies have implemented offline dissolved gas analysis (DGA) as a condition monitoring technique. This involves manually taking oil samples periodically and sending them to a lab to check for dissolved fault gases like hydrogen, methane, ethylene, etc. While DGA can detect developing faults, it provides just a periodic snapshot in time and requires extensive labor. Faults can develop rapidly between sample intervals and go undetected until too late.
Traditional multi-gas online DGA monitors have their own pitfalls.
- Cost – these cart-sized analyzers are extremely expensive, costing $50,000-100,000 or more per unit.
- Maintenance – multi-gas DGA monitors require frequent, costly maintenance and calibration. There are anecdotes indicating some utilities just unplug them after 4-5 years to avoid the cost of maintenance.
- Limited deployment – due to high costs, utilities often can only afford to install on a small fraction of their transformer fleets.
- Complexity and size – often large and complex, installation and integration into existing systems are more challenging.
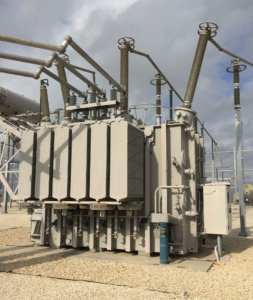
transformer fleet with
affordable and reliable
hydrogen sensors.
The prohibitive cost of these DGA monitors is probably the largest pitfall that forces utilities to install them on a fraction of the transformers operated, in some cases just 10% of the transformer fleet. This supplies scant protection with a high potential cost of replacement should failure occur, when these transformers can cost $5 million or more.
The H2scan Solution – Early Hydrogen Sensor Warning at a Fraction of the Cost
There is a much more cost-effective and lower maintenance solution for online transformer fleet monitoring – hydrogen-specific fault gas detection. H2scan has pioneered hydrogen sensor technology by developing a patented, solid-state sensing element able to provide reliable, maintenance-free monitoring with an anticipated lifespan of ten years or more at just a fraction of the cost of multi-gas analyzers.
While multi-gas units analyze a handful of different gases, detecting hydrogen alone is sufficient to provide early warning of transformer faults. Hydrogen is a key fault gas that is generated by virtually every type of transformer fault, including thermal faults, partial discharge and arcing. As hydrogen levels rise, problems that should be further diagnosed and addressed are indicated.
With H2scan hydrogen sensor technology, facility managers or maintenance teams get an affordable “check engine” light that alerts when a transformer is actively faulting. Instead of running transformers to failure, utilities or companies can practice true predictive maintenance. Early and swift identification of an issue allows time to plan for a repair or replacement to forestall catastrophic failure.
What Type of Transformers Can Benefit from H2scan’s Hydrogen Sensor Monitoring?
H2scan sensors can be used for all different types and sizes of transformers, such as distribution, transmission, substation, wind turbine and industrial transformers. The solid-state sensors are extremely compact and can be easily installed on both new and existing assets with minimum disruption. When utilities only monitor a fraction of the fleet of larger “critical” transformers, a cost-effective single-gas sensor providing real-time, continuous monitoring enables companies and utilities alike to protect transformers of any size.
Start Predicting Your Failures Today for Successful Power Management
In today’s environment of aging infrastructure, increasing energy demands and scarce skilled labor resources, it is too costly in terms of time and money to have key assets like transformers failing unexpectedly. Implementing affordable online hydrogen monitoring provides the advanced warning needed to move to a predictive maintenance strategy that maximizes transformer reliability and uptime.
Don’t get caught by surprise. Contact H2scan today to learn how its transformer monitoring solutions can help you predict your next failure and avoid costly disruptions.