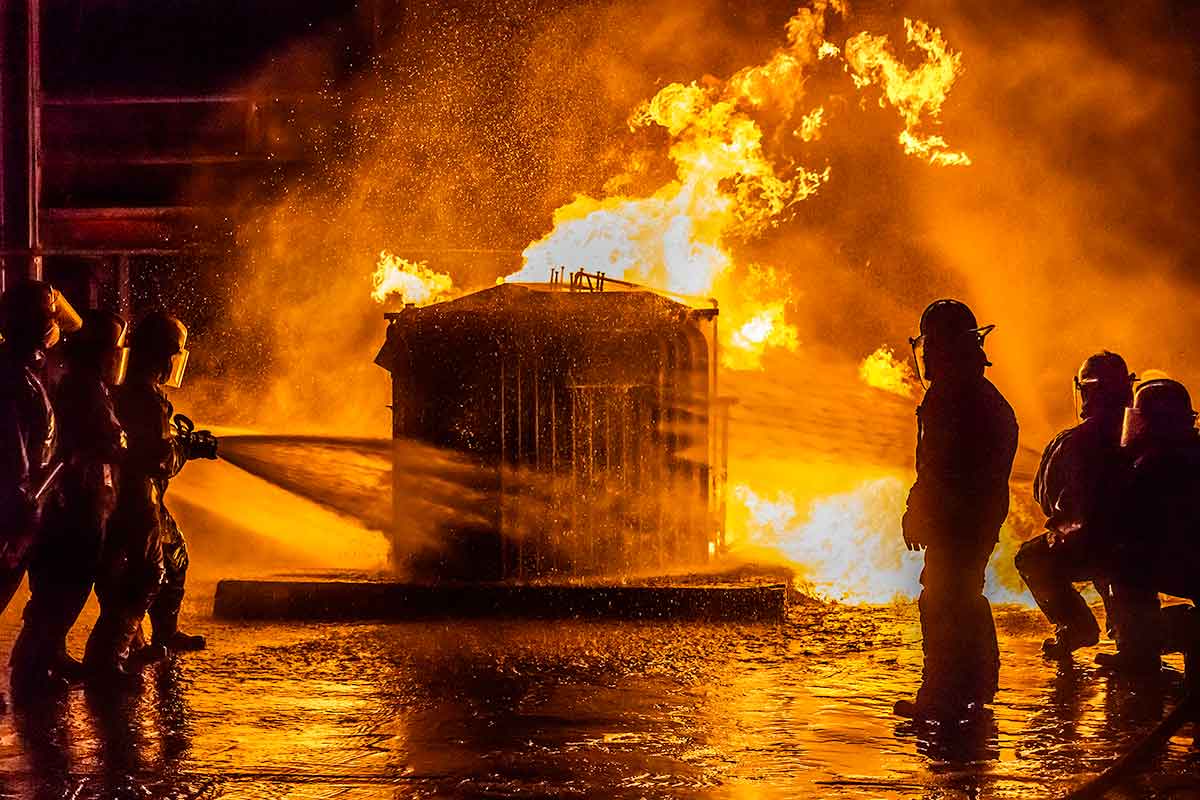
Causes of Power Transformer Failures in Industrial Applications
Power transformers are critical to industrial operations, regulating voltage levels to ensure the efficient distribution of electricity for various processes. Their reliability is essential, as failures can lead to costly downtime, equipment damage, and safety hazards. However, transformers are susceptible to electrical faults, thermal stress, mechanical wear, environmental conditions, and improper maintenance, all of which can compromise performance. This blog explores these major failure causes and their impact on industrial settings, providing insights into risk mitigation strategies that can enhance transformer longevity and prevent unplanned outages.
Electrical Faults
Electrical faults are among the most common causes of transformer failures in industrial applications. These faults can occur due to several reasons:
- Overvoltage Conditions: Power transformers are designed to handle specific voltage levels. However, events such as lightning strikes, switching surges, or grid disturbances can lead to overvoltages that exceed the transformer’s insulation capacity. This can cause insulation breakdown and subsequent failure.
- Short Circuits and Ground Faults: Short circuits, whether phase-to-phase or phase-to-ground, can generate excessive currents that cause localized heating within the transformer windings. Over time, this heating can degrade the insulation, leading to a breakdown. Ground faults can also lead to similar outcomes, especially in systems with weak grounding or poor protection mechanisms.
- Harmonics and Transients: Industrial environments often generate electrical harmonics due to the operation of variable frequency drives, large motors and other nonlinear loads. These harmonics can cause additional heating and stress on the transformer windings.
- Transient Overvoltages: such as those from capacitor switching or fault clearing, can also stress the insulation, leading to failure over time.
Thermal Stress
Transformers generate heat during operation that must be effectively managed to avoid thermal stress:
- Overloading: Operating a transformer beyond its rated capacity causes excessive heating. Even if the overloading is intermittent, the cumulative effect can accelerate insulation aging and lead to premature failure.
- Excessive Harmonics: Harmonics create circulating (eddy) currents in the transformer core, resulting in heating even when the transformer is not fully loaded. Monitoring and filtering harmonic content mitigate this cause of premature aging.
- Cooling System Failures: Transformers rely on cooling systems, such as oil circulation or forced air cooling, to dissipate heat. Failures in these systems, whether due to mechanical faults, coolant leaks, or fan issues, can result in overheating. Prolonged operation under high temperatures degrades the transformer’s insulation and can cause catastrophic failures.
- Ambient Temperature Variations: Industrial transformers often operate in environments with fluctuating ambient temperatures. Temperature variations can reduce the cooling efficiency of the transformer, impacting circulation and the ability of the transformer to dissipate heat. Seasonal temperature changes can affect the natural thermal cycling process in power transformers. These effects stress the insulation systems and other components.
Mechanical Issues
Mechanical issues often arise due to physical stress, manufacturing defects, or operational mishaps:
- Winding Deformations: During operation, electromagnetic forces can cause the windings to move slightly. Over time, this movement can lead to deformation, reducing the transformer’s ability to withstand short-circuit forces. Mechanical shocks, such as those from transport or installation, can cause winding deformation, leading to internal faults.
- Core Loosening and Vibrations: The core of a transformer is crucial for efficient operation. However, mechanical vibrations, whether from external sources or internal issues, can lead to core loosening. A loose core can create hotspots, reduce efficiency, and eventually cause failure.
- Structural Weaknesses: Poor manufacturing practices, such as improper clamping of windings, loose fasteners, or inadequate design, can lead to structural weaknesses in a transformer. These weaknesses may not be immediately apparent but can lead to failures under operational stress.
Environmental Conditions
Environmental factors can significantly impact transformer performance:
- Moisture Ingress: Transformers are designed to operate in a dry environment, but moisture can enter through seals, gaskets, or through condensation. Moisture reduces the dielectric strength of the insulation(and premature aging of the paper), leading to partial discharges and eventual failure.
- Contaminants and Pollution: Industrial environments often expose transformers to pollutants like dust, dirt, and chemicals. These contaminants can accelerate aging by degrading insulation or clogging cooling systems, leading to overheating.
- Corrosion: Corrosion is a significant issue in environments with high humidity, salt, or chemical exposure. It can affect the transformer’s metal components, leading to leaks, structural weakening, and eventual failure. Protective coatings and regular maintenance are essential to mitigate this risk.
Improper Maintenance
Regular maintenance is crucial for the longevity of power transformers:
- Lack of Routine Inspections: Routine inspections help identify potential issues before they become serious problems. Without regular inspections, issues such as oil degradation, insulation wear, or mechanical defects can go unnoticed until they cause a failure.
- Incorrect Repairs and Retrofitting: Using non-standard parts or improper repair techniques can compromise transformer reliability. Unauthorized retrofitting can introduce new failure modes, especially if not done following manufacturer guidelines.
- Inadequate Monitoring Systems: Modern monitoring systems, such as Dissolved Gas Analysis (DGA) and thermography, provide valuable real-time insights into transformer health. Relying solely on manual inspections without incorporating these technologies can lead to undetected issues, increasing the risk of failure.
Case Studies and Real-World Examples of Industrial Transformer Failures
Examining real-world transformer failures provides insights into the contributing factors and preventive measures:
- Case Study 1: Transformer Failure Due to Overloading: An industrial facility experienced a transformer failure after consistently operating the transformer at 120% of its rated capacity. The overloading led to insulation degradation, ultimately causing a catastrophic failure. The facility implemented stricter load management practices and upgraded to a higher-capacity transformer. Continuous DGA monitoring could have detected the degradation earlier and avoided the outcome.
- Case Study 2: Environmental Impact on Transformer Longevity: A transformer located in a coastal industrial area failed due to severe corrosion caused by salt exposure. Regular inspections and the application of protective coatings were insufficient. After the failure, the facility installed transformers with enhanced corrosion resistance and improved maintenance protocols.
Understanding the causes of power transformer failures in industrial applications is essential for improving reliability and preventing costly downtime. The primary causes include electrical faults, thermal stress, mechanical issues, environmental conditions, and improper maintenance. Implementing preventive measures such as regular inspections, proper maintenance, environmental controls, and continuous monitoring can significantly reduce the risk of transformer failures.
Ready to discuss protecting your industrial transformers? Contact us to talk to one of our application engineers.
References
- IEEE Standard C57.91-2011, “Guide for Loading Mineral-Oil-Immersed Transformers.”
- P.M. Anderson and A. A. Fouad, “Power System Control and Stability,” Wiley-IEEE Press, 2002.
- D. K. Paliwal, “Transformer Failures, Causes & Remedies,” Power Systems Engineering Research Center, 2003.
Traci Hopkins is Sales Manager for Latin America at H2scan Corporation, a world-class hydrogen sensor solutions provider. Hopkins has authored numerous papers for various publications within the utility industry and has presented on the topic of transformer reliability on numerous occasions at national engineering conferences. Hopkins has worked with maintenance and reliability professionals across six continents. She currently focuses on bringing specialized hydrogen monitoring expertise to Latin American utility markets.