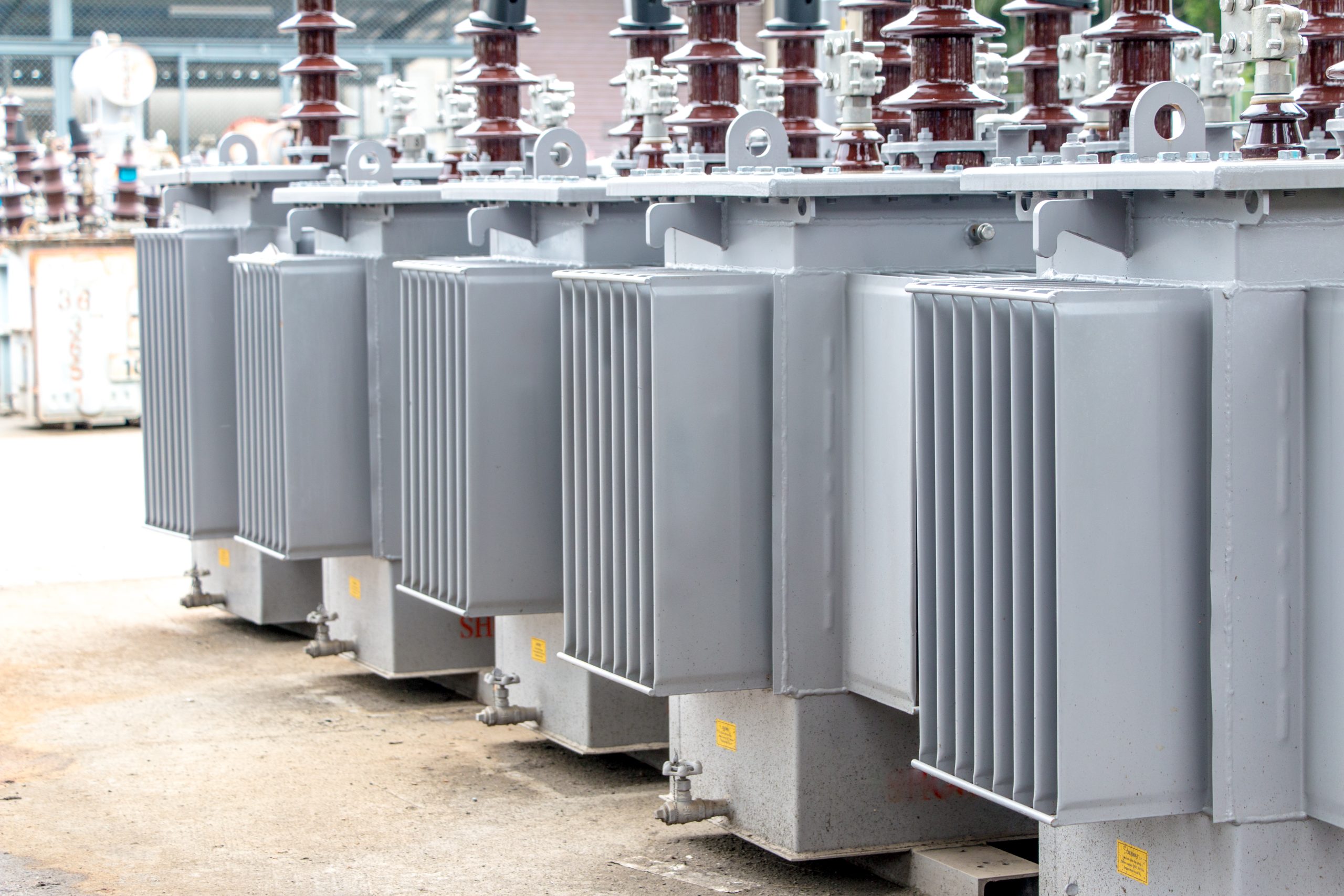
Mitigating Transformer Aging: The Critical Triad of Heat, Moisture and Oxygen
The power sector is currently grappling with a triple threat; transformer supply chain disruptions, rising costs and aging in-service transformers. Currently, lead times for large transformers have surged to 120 to 210 weeks (about 4 years), in a stark increase from the 30-60 weeks potential delivery times pre-pandemic. At the same time, raw material commodity prices have driven up transformer prices anywhere from 60-80% on average since January 2020 (depending on the size and application).
Compounding this crisis, the average age of in-service large power transformers (LPTs) in the U.S. is 38 years—near or even past their design lives, according to a 2020 study by the U.S. Dept. of Commerce. In this context, extending the lifespan of existing transformers through careful monitoring and maintenance has become increasingly crucial.
Utilities and companies interested in extending transformer lifespan to preserve capital equipment and protect the power grid should consider three primary factors that accelerate transformer aging: heat, moisture and oxygen. Understanding and managing these elements can significantly extend transformer longevity and reliability, potentially alleviating some of the pressure on the strained supply chain.
The Aging Triad: Heat, Moisture and Oxygen
Heat: The Silent Accelerator
- Temperature plays a crucial role in transformer aging. According to an academic source that published a guide about applied maintenance for half-century transformers, a 10°C top oil temperature increase doubles the rate of hydrocarbon oxidation reactions. This acceleration occurs regardless of other factors present, underscoring the importance of temperature control.
- Heat not only directly impacts insulation breakdown but also indirectly affects cooling efficiency. As transformer oil ages and oxidizes, it develops acids and sludges, increasing its viscosity. This thickening reduces the oil’s ability to transfer heat effectively from the core to the tank walls, causing the transformer to run hotter and work harder, further accelerating the aging process.
Moisture: The Pervasive Threat
- Moisture in transformers is a persistent challenge. It can originate from various sources including inadequate drying at the factory, improper installation, insufficient drying of new oil during commissioning, cellulose (paper insulation) breakdown and environmental ingress due to poor manufacturing or maintenance practices.
- Water, chemically bonded to both oil and paper insulation, may be released during operation. As oil oxidizes over time, it can create excess water along with other oxidation decay products. The presence of moisture accelerates oxidation processes and the breakdown of both oil and paper insulation.
Oxygen: A Secondary Consideration
- While oxygen plays a role in transformer aging, its direct measurement is often not as critical as monitoring heat and moisture. At top oil temperatures of 70°C or above, oil can start to oxidize even without free oxygen present, highlighting how heat is the primary catalyst in this process. Moreover, oxygen ingress is often a symptom of poor sealing or maintenance issues, which are typically detected first through moisture monitoring.
- Transformer oils contain natural inhibitors that react with oxygen. Regular testing of inhibitor levels during annual oil analysis can indicate oxygen ingress. If inhibitor levels decrease rapidly, it suggests higher oxygen presence.
The question remains on how utilities and power engineers can monitor all three aging factors across their entire transformer fleet.
Hydrogen Sensors that Double Duty for Heat and Moisture Monitoring
The GRIDSCAN™ 6000 Multi-Sense Monitor from H2scan focuses on measuring heat and moisture, to provide a cost-effective and efficient way to manage oxygen-related issues. By closely monitoring temperature and moisture levels, many of the problems associated with oxygen can be preemptively addressed, negating the need for direct oxygen measurement in many cases.
Transformer design also plays a role in oxygen management:
- Free-breathing transformers: saturated with air typically have around 30,000 ppm oxygen
- Sealed Nitrogen-blanketed transformers: around 3,000 ppm oxygen
- Vac-filled transformers with a continuous N2 system: as low as 300 ppm oxygen
Transformer Design and maintenance practices are important to limit the rate of oxidation. Many sealed transformers have become “free-breathers” due to a variety of factors such as leaks, improper installation, and deteriorated gaskets that allow oxygen and moisture to enter the transformer. Oil preservation systems such as a continuous N2 system or conservator with a good bladder help to control oxygen and moisture ingress.
Maintenance Practices for Longevity
Some tips for operators interested in extending the lifespan of the transformer fleet include:
- Regular visual inspections are crucial for identifying potential issues early. These inspections should include checking for cracks in welds, especially on radiators, inspecting and replacing gaskets as needed and identifying and addressing leaks promptly.
- Oil quality management is another critical aspect of transformer maintenance. Regular oil quality tests (acidity, interfacial tension, color, particle count) should be conducted. When quality deteriorates, oil reclamation should be considered, with oil replacement as an option in severe cases such as the presence of Corrosive Sulphur.
- Load management is essential for preventing overheating. Transformer loading should be monitored and managed, with load reduction considered if consistent high temperatures are observed.
- Inhibitor management involves testing for and maintaining adequate levels of oxidation inhibitors like 2,6 ditertiary-butyl paracresol (DBPC). Adding inhibitor, re-inhibiting, as needed can protect the insulation against oxygen-related degradation by reacting with the oxygen that is in the oil.
- Moisture control is crucial and involves addressing leaks and ingress points promptly, as well as implementing drying procedures when moisture levels exceed acceptable limits.
When considering the triple threat facing the power industry, in this challenging environment, the GRIDSCAN 6000 Multi-Sense Monitor can help address those concerns. By focusing on the two most critical factors – temperature and moisture – this system allows utilities to monitor more transformers across their fleets for the same or similar cost as monitoring a single transformer with more comprehensive systems. This broader coverage is particularly crucial given the average age of large power transformers (38 years) and the need to extend their operational lives. While comprehensive gas analysis solutions including oxygen measurement are available, their prohibitive costs can limit widespread deployment, potentially leaving critical assets unmonitored.
Effective transformer management doesn’t necessarily require direct measurement of all three aging factors (heat, moisture and oxygen). By strategically monitoring temperature and moisture with the GRIDSCAN 6000 Multi-Sense Monitor, combined with proactive maintenance practices and indirect oxygen assessment, utilities and power engineers can significantly extend transformer life. This approach, coupled with comprehensive maintenance strategies, enables effective safeguarding of these critical assets’ longevity and reliability across an entire fleet, ultimately enhancing overall grid resilience and performance.
H2scan is a leading developer and manufacturer of high-performance hydrogen sensors for transformer fleet management, hydrogen processing and safety monitoring.