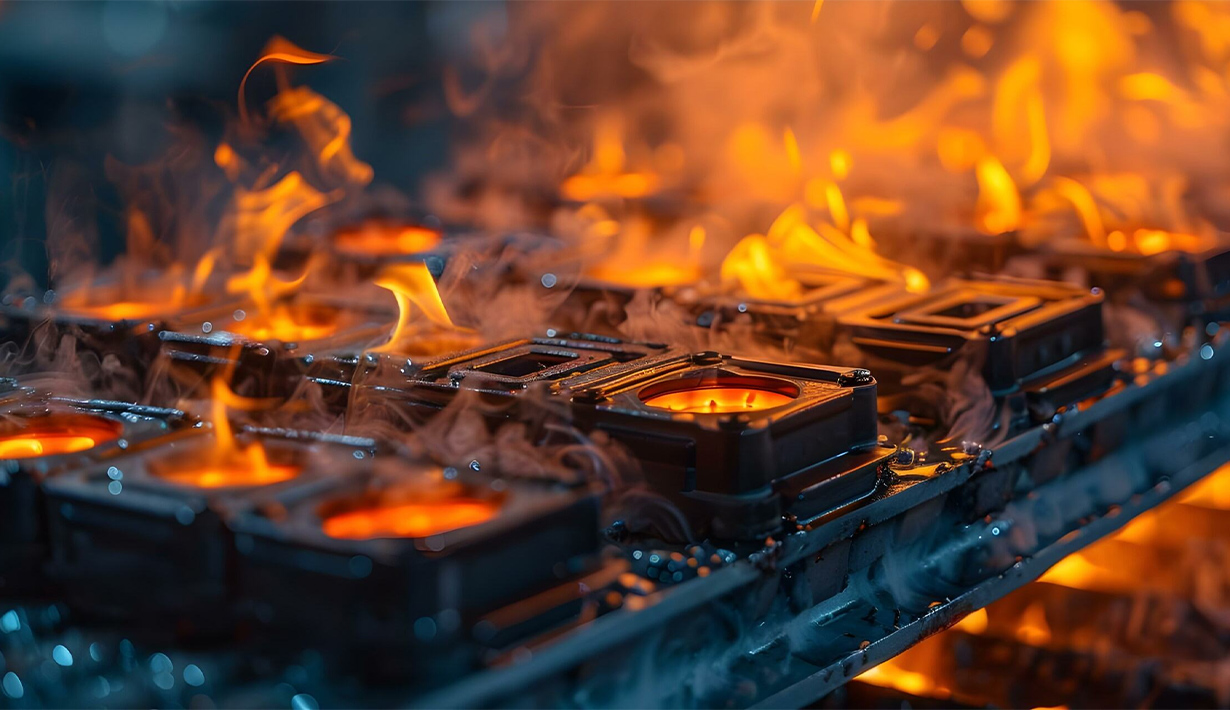
Why Hydrogen Detection Is a Must-Have in Your Li-Ion Battery Management System
So, you’ve been told you need a Battery Management System (BMS) for lithium-ion batteries — maybe for a new battery installation, an energy storage project or to meet evolving safety standards. The BMS acts as the brains of the battery system: to monitor performance, keep charging and discharging within safe limits and shut things down when needed.
But here’s something you might not have been told: among the various gas types present under abnormal conditions, one single gas is more important than all the rest for monitoring. Hydrogen detection isn’t just helpful — it’s essential. And it should be part of any modern, reliable BMS setup.
Why Hydrogen Matters in Lithium Battery Management Safety
Under normal conditions, lithium-ion batteries don’t emit hydrogen gas. However, when something goes wrong — such as overcharging, cell damage, separator defects, internal short circuits, or even tiny lithium dendrites forming inside the battery — the battery can enter a state known as thermal runaway. That’s when things get dangerous fast.
In thermal runaway, temperatures rise uncontrollably at a rate of 20°C per minute, with the critical temperature 125°C, and can go as high as 500°C. This extreme heat causes the separator inside the battery to melt, compromising the critical Solid Electrolyte Interphase (SEI) layer. The SEI layer is fundamental to battery operation, as it facilitates lithium-ion movement while restricting electron flow. When this layer degrades, the battery chemistry becomes increasingly unstable and breaks down.
One of the main byproducts of this breakdown? Hydrogen gas — along with carbon monoxide, carbon dioxide and other toxic or flammable gases.
Research has shown that hydrogen becomes the primary gas released during the early stages of thermal runaway, making it an ideal early warning indicator. As temperatures continue to rise above 200°C, the anode becomes exposed, which accelerates the decomposition process. By 300°C, the cathode materials begin to break down, significantly heightening the chances of deflagration and explosions.
However, the main gas generated, hydrogen, is especially dangerous because:
- It’s highly flammable
- It’s odorless and invisible
- It can accumulate in confined spaces
- Just a small concentration can ignite
Without proper detection and continuous monitoring, you could have a dangerous situation building, without any warning until it’s too late.
The Role of the Battery Management Systems — and Where Hydrogen Detection Fits In
Safety begins with the Battery Management System (BMS), also known as the Energy Storage Management System (ESMS). The BMS monitors essential battery performance indicators, such as charging status, state of charge, over-discharging and temperature levels. When the BMS detects conditions that could lead to a hazardous situation, it promptly shuts down the system. Furthermore, the BMS optimizes battery performance to ensure maximum efficiency, longevity and overall functionality.
Modern BMS systems can detect conditions that might lead to thermal events, but they cannot directly sense the presence of hydrogen that indicates a thermal runaway has already begun.
While the BMS handles charging, balancing and temperature monitoring to be fully protective, a Battery Management System must include hydrogen gas detection. When integrated into your BMS, hydrogen sensors act as the first line of defense. They detect early-stage gas buildup before things escalate. That gives your system time to:
- Trigger alarms
- Power down battery modules
- Turn on ventilation
- Alert personnel
- Prevent fire or explosion
It’s the missing piece that bridges electronic control with real-world hazard mitigation.
Why Regulations Now Require Hydrogen Detection
Safety codes and standards around the globe are beginning to require hydrogen detection and organizations can anticipate insurance coverage to reflect these standards. Numerous regulations and safety standards mandate the use of hydrogen detection systems in battery rooms or locations housing lithium batteries.
- NFPA 855 mandates detection systems of combustible gases (like hydrogen) in energy storage systems
- UK COSHH regulations require employers to assess risks associated with hazardous substances like hydrogen and to establish action plans for accidents, incidents, or emergencies.
- IEC 62933-5-2 provides recommendations for ESS safety, including gas detection systems for early warning of thermal events
- UL 9540A test methods evaluate thermal runaway propagation in battery energy storage systems, with results often driving requirements for gas detection
Many local fire marshals and insurance policies now require gas detection systems as part of lithium storage room design
Bottom line: If you’re installing lithium batteries, hydrogen detection is expected and often required for battery management system for lithium ion batteries.
The Smart Way to Integrate Hydrogen Detection
Not all gas sensors are created equal — and many weren’t designed for lithium battery environments. That’s where H2scan comes in.
H2scan’s technology represents a significant advancement compared to traditional electrochemical or catalytic bead sensors in several critical ways. Our sensors provide precise measurements without interference from other gases common in battery installations, thanks to a hydrogen-specific precious minerals alloy that selectively absorbs hydrogen molecules.
Traditional sensors often require quarterly calibration, replacement of sensing elements every 1-2 years and are susceptible to drift and false alarms. In contrast, H2scan sensors maintain accuracy throughout their 10+ year lifespan without any of these issues. This drastically reduces maintenance costs, eliminates unnecessary visits and prevents the risks associated with sensors that have drifted out of calibration. Our continuous monitoring capabilities provide early insight into battery conditions, allowing costly and unforeseen failures to be avoided.
- Our patented solid-state hydrogen sensors are designed for:
- Zero maintenance — auto-calibrating with no calibration gases or site visits unless abnormalities are detected
- 10+ year lifespan — matches your battery system’s lifecycle
- Fast, accurate response — detects even low hydrogen levels early
- Easy integration — works with your existing PLC, BMS or alarm systems
- Self-diagnosing — alerts you to any operational issues automatically
With H2scan’s HY-ALERTA® 5020 general location sensor or the HY-ALERTA® 5320 intrinsically safe sensor with 4-20mA and Modbus or Modbus RTU capabilities in a NEMA 4X enclosure, you’re not just ticking a compliance box — you’re adding a trusted layer of safety with our market-leading Gen 5 technology.
Final Thought: A Smarter Battery Management System Includes Hydrogen Detection
Your Battery Management System is the control center. But without hydrogen detection, it’s blind to one of the most dangerous signs of failure. Don’t let a preventable gas buildup turn into a catastrophic event. With reliable hydrogen sensing integrated into your system, you gain early insight into abnormal conditions, allowing you to prevent damage to your equipment, your facility and most importantly, ensure the safety of your personnel. This same insight allows operations teams to migrate to condition-based maintenance strategies, avoiding unnecessary costs typical of periodic maintenance regimes.
Sources:
- NFPA 855: Standard for the Installation of Stationary Energy Storage Systems: https://www.nfpa.org/codes-and-standards/all-codes-and-standards/list-of-codes-and-standards/detail?code=855
- UK COSHH Regulations: https://www.hse.gov.uk/coshh/
- IEC 62933-5-2: Electrical Energy Storage Systems Safety Requirements: https://webstore.iec.ch/publication/30966
- UL 9540A: Test Method for Evaluating Thermal Runaway Fire Propagation in Battery Energy Storage Systems: https://www.ul.com/services/9540a-test-method
- Feng, X., et al. (2018). “Thermal runaway mechanism of lithium ion battery for electric vehicles: A review.” Energy Storage Materials, 10, 246-267: https://www.sciencedirect.com/science/article/abs/pii/S2405829716303453
- Kong, L., et al. (2018). “Gas evolution behaviors for several cathode materials in lithium-ion batteries.” Journal of Power Sources, 396, 358-367: https://www.sciencedirect.com/science/article/abs/pii/S0378775318304377
- Lee, J.Y., et al. (2024). “A study on the mitigation method of thermal runaway in lithium-ion battery energy storage systems using numerical analysis.” Journal of Energy Storage, 76, 109812: https://www.sciencedirect.com/science/article/abs/pii/S2352152X24007461
Gas component | Concentration % (v/v) |
---|---|
CO₂ | 20.39 |
CO | 5.39 |
N₂ | 27.06 |
O₂ | 0.02 |
H₂ | 34.35 |
CH₄ | 4.50 |
C₂H₄ | 3.58 |
C₂H₆ | 1.06 |
C₃H₆ | 0.93 |
C₃H₈ | 0.29 |
C₄H₈ | 0.37 |
C₄H₁₀ | 0.12 |
Jeff Donato is Sales Director of Safety Products at H2scan Corporation, a world-class hydrogen sensor solutions provider. Donato is an IEEE PES member and Chair of Working Group 1578, bringing technical standards expertise to the industry. Donato previously served as Chief Technology Officer and Chief Marketing Officer at EnviroGuard and possesses deep experience in the standby battery industry, critical to power systems and safety applications.